Vinyl Technology's Storied History Spans Five Decades
1960’s
The company’s founders, Carlos Mollura Sr., a degreed engineer, and his wife, Haydee, immigrate to the U.S. from Argentina in 1963, hungry to make their mark in the land of opportunity. Four years later they open their first company, Quality Vinyls(QV) in South El Monte, CA, with a $1500 investment and a 3200 ft² building. Carlos works as a one-man shop making above ground pool liners. Shortly thereafter, QV lands its first government contract with the GSA for vinyl portfolios. Moving into the 70’s, the company begins to grow, diversify, and incorporates.
1970’s
The 70’s are a very busy decade for QVC. In 1970, the company gains international visibility at the 1970 World’s Fair in Osaka, Japan. QVC manufactures the light sculpting parasols, bringing to fruition the architect’s and designer’s vision of 5 spinning kaleidoscopes as the working center pieces in the Canadian Pavilion at Expo ‘70. The beautiful spinning parasols reflected light creating ambiance and mood within the open air pavilion.
In 1972, QVC is contracted to make the Level-B Hazardous Material suits for the Rocky Flats Plant clean-up effort. Production of those radioactive material resistant suits continues for over 10 years.
1974 brings more product manufacturing diversity along with a name change. QVC changes its name to Mollura Industries (MI) to market a successful proprietary waterbed line. It does this while continuing to draw attention at another World’s Fair, Expo ‘74 in Spokane, WA. Under its new name, MI quickly gains international recognition by manufacturing large flying foam insects over the US Recycling Pavilion.
The following year, in 1975, MI relocates to City of Industry purchasing a new 150,000 ft² building and custom designs 2 large-scale 50kw RF Welding machines to build upon the capacity needed to keep up with its waterbed demand. In 1979, Carlos Sr. receives a patent for the first waveless waterbed, The Innercoil.
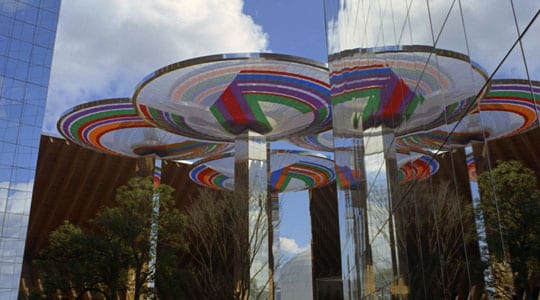
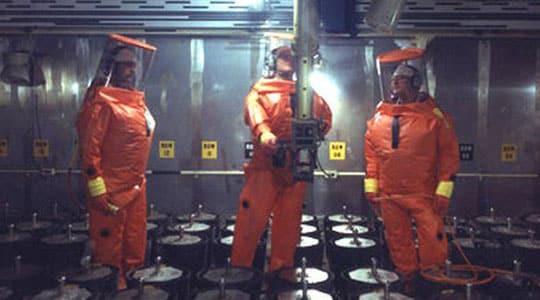
1980’s
The 80’s is again a decade of transition. It starts with the end of a successful era in waterbeds. Mollura Industries receives honors for Best in Show at the Waterbed Manufacturer’s Show in 1981. But later the same year, Mollura Industries closes down due to financial challenges as the water bed industry begins to move off-shore and MI re-emerges as Vinyl Technology, Inc. (VTI).
Just 4 years after VTI’s inception it is nominated “Outstanding Small Business Subcontractor of the Year” by Rockwell International. Then 4 years later in 1989, VTI breaks into the Hispanic 500 list of top Hispanic owned companies, ultimately breaking into the top 200 in 2010.
VTI also enters the medical products arena in the 80’s winning a contract to produce military anti-shock trousers used to treat severe blood loss or pelvic fractures on the battlefield.
1990’s
Demand for VTI’s manufacturing services continues to grow into the 90’s with increased production forcing expansion into off-site facilities. In 1992, VTI moves to its current facility in Monrovia, CA.
In 1993, VTI was voted “Small Minority Business Subcontractor of the Year” by Lockheed Space Operations for its contribution to the Space Shuttle program. VTI manufactured part of the Sound Suppression Water System that counters the damaging effects of the reverberating acoustics caused by the Solid Rocket Boosters.
In the mid 1990s, VTI is contracted to manufacture the Demilitarization Protective Ensemble (DPE), a Level-A Haz Mat suit that protects against chemical exposure from nerve and mustard agent in the effort to clear stockpiled chemical weapons. To this day VTI continues as the sole manufacturer of the DPE.
1999 brings new technology and more growth. VTI opens Universal Plastifab, Inc., as a wholly owned subsidiary to offer acrylic fabrication and thermoforming of rigid plastics. In the same year, VTI automates its business operating system choosing (what is now known as) Epicor Software Company to deliver its first ERP system.
2000’s
The new millennium brings more change as well as a solid start in the aerospace business and a breakout contract for high volume industrial sewing.
VTI receives Boeing Quality System approval in 2002 in pursuit of their insulation blankets. Then, in 2003, VTI is chosen as a subcontractor in support of the I-GNAT UAV, manufacturing its first collapsible fuel bladders specifically for UAV’s.
In 2005, VTI turns over leadership of the company to the second generation of Mollura’s and welcomes Dan Mollura as the new President. Carlos Sr. remains on as Chairman of the Board and trusted advisor.
2005 is also the year VTI becomes the first U.S. company qualified to manufacture the Advanced Technology Anti-Gravity Suit (ATAGS), which it continues to manufacture for the U.S. Air Force and Navy.
In 2007, VTI invests in an Eton Material Handling system to support a large multi-year contract for sewn military bags. The system automates handling and delivery of textiles directly to operator stations for large scale industrial sewing operations.
In 2008, VTI’s quality system is certified to the ISO9001 standard, which opens the door for additional business opportunities from those customers and industries that require it.
2010’s
The current decade brings improved technical competence and structure as the company becomes more engineer-centric to move into more technically demanding new business applications. Manufacturing and integration support of UAV fuel systems rise to a new level and VTI is up for the challenge, developing new manufacturing processes and facilitating integration which continues today.
Research and Development efforts also increase in 2010 as VTI develops, among other things, a new proprietary bonding process to complement its core processes across multiple applications.
In 2013, Universal Plastifab is sold off to focus on VTI’s emerging new markets requiring its core competencies of RF Welding and Industrial Sewing.
In 2014, VTI implements Lean-Six Sigma methodologies to improve operations—training key staff as Six Sigma Green Belts and hiring Six Sigma Black Belts to key positions.
In 2016, VTI is awarded additional contracts to manufacture Cargo Transfer Bags for the International Space station.
In 2017, VTI received AS9100D which allowed it to pursue more aerospace contracts.